First Things First!
Looking for suppliers? Check out this curated worldwide list of MYOG fabric suppliers before you go any further. A smaller selection of suppliers are provided in this article.
Choosing the right fabric can feel overwhelming, but it doesn’t have to be. Forget the endless specs and marketing jargon for a moment. The most expensive, high-tech material isn’t always the best tool for the job.
For example, a 420 denier nylon is often tougher and more abrasion-resistant than a more expensive “ultralight” laminate like X-Pac VX21, at about the same weight. The trade-off? X-Pac is crisper, easier to sew, and more waterproof. Your project’s needs—not the hype—should drive your choice.
The Core Principles of Gear Fabrics
Before we dive into specific materials, let’s establish some ground rules. Keep these principles in mind, and you’ll be 90% of the way to making a great choice.
- Denier & Weight: A higher denier (D) number means thicker threads. Generally, a heavier fabric (measured in oz/yd² or g/m²) is stronger, but the type of fiber matters more.
- The Fiber Hierarchy: For the same weight, fibers generally rank in strength like this: Polyester < Nylon < High-Tenacity Nylon (like Robic or Cordura) < Ultra-High-Molecular-Weight-Polyethylene (UHMWPE, the stronger than steel fibres in Dyneema®). Cotton is rarely used anymore outside of a few heritage brands and should generally be avoided.
- Nylon vs. Polyester: Nylon is king for strength and abrasion resistance. Polyester however has superior UV resistance and holds color better, making it great for printed fabrics and gear that lives in the sun. It also doesn't stretch and sag when wet.
- Ripstop Grids: That checkerboard pattern on many fabrics is a grid of thicker, stronger threads woven in to stop small tears from becoming catastrophic failures.
- Water Resistance vs. Waterproofing:
- DWR (Durable Water Repellent): This is the coating that makes water bead up and roll off. The industry is shifting from C6 (a durable but problematic PFAS "forever chemical") to the less-durable but hopefully safer C0. DWR always wears off, causing fabric to "wet out"-but that doesn't mean it's no longer waterproof, because...
- The Real Waterproofing is Inside: Most fabrics rely on a coating on the "wrong" side. PU (polyurethane) is extremely common and lasts 5-10 years before flaking. Cheap fabrics might use heavy, nasty PVC (avoid it). High-end fabrics like XPAC laminate a thin plastic film to the material, while ultralight tent and dry bag fabrics often use a silicone coating.
- Tame the Fray: Coated and laminated fabrics are a dream to work with because they fray less. For uncoated fabrics, always seal the cut edges (carefully with a flame, or by binding them) to ensure your gear lasts.
- Weight Savings: The fastest way to an ultralight pack isn't always a high-tech fabric. It's smart design. Removing unnecessary features and using less material will always be the cheapest way to shed grams.
Fabrics by Use Case
Here are some of the best and most common fabrics, grouped by use case. See our comprehensive patterns for many projects to make with these fabrics.
Ultralight Shelters, Dry Bags and Internal Liner Fabrics
When every gram counts and waterproofness is non-negotiable. See this article on seam-sealing if you are looking into making dry bags or waterproof liners.
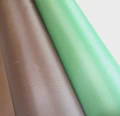
Silicone-Coated Polyester (Silpoly) or Nylon (Silnylon)
The go-to choice for modern ultralight tarps and tents. Silpoly absorbs almost no water, meaning it won't sag overnight when damp like its nylon counterpart. It's waterproof, affordable, and reasonably durable for its weight. A 1.1 oz/yd² (or ~20D, 40gm²) version is often the sweet spot for shelters. up to 2 oz/yd² (70D, 70g/m²) is often used for burlier dry sacks.
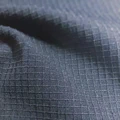
PU-Coated Nylon/Polyester
The most common fabrics used for dry bags, internal linings and tents. Low priced, very strong and seam-tapeable. Usually used at similar deniers/weights as the silicone-coated fabrics described above.
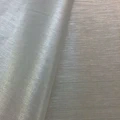
Dyneema® Composite Fabric (DCF)
Formerly Cuben Fiber, DCF is the gold standard for ultralight performance. It's a non-woven laminate of UHMWPE fibers and polyester films. It is 100% waterproof, does not stretch, and is crazy strong for its low weight. It's also very expensive and is generally less packable than a silpoly/nylon alternative. Weights around 0.5 to 1.0 oz/yd² are common for shelters and bags.
Backpacks & Bike Bags
This is where things get burly. Pack fabrics range from 210D for ultralight builds to 1000D for bombproof bags. A great strategy is to mix and match: use a lighter fabric for the main body and a tougher one for high-wear areas like the base.
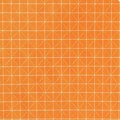
210D Nylon (Robic, Gridstop, Ultragrid)
The sweet spot. These fabrics typically offer the best balance of strength, weight, and cost for many backpack and bike bag projects. Ripstop variations are preferred, for example Robic® uses stronger Nylon 6.6, while Ultragrid® weaves in UHMWPE for significantly higher tear resistance. When you try cutting your fabric you will appreciate the extra cost.
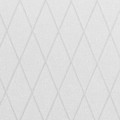
XPAC VX21 / ECOPAK EPX200
The iconic waterproof laminate. These fabrics sandwich a ripstop grid and a waterproof film between a face fabric (210D in this case) and a backing. They are stiff, edge stable (no fraying), and don't absorb water, making them easy to sew. Ecopak is a increasingly popular eco-friendly alternative made from recycled polyester. Many stronger and lighter weight variants exist to suit your project.
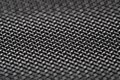
Challenge ULTRA 200/400
The current king of strength-to-weight. ULTRA is a woven fabric made almost entirely from UHMWPE, laminated to a waterproof film. It's ridiculously strong: the 400D version survived being dragged by a car. It's also extremely expensive and requires some care with the construction techniques as there are reports of delamination, especially in earlier versions of the fabric.
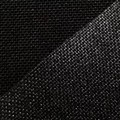
500D-1000D Cordura Nylon
The classic choice for bombproof gear. This is what tactical bags and heavy-duty luggage are made of. It has a textured, matte finish and great abrasion resistance. Use 500D for a tough but not too heavy pack or 1000D for high-wear areas and tactical gear.
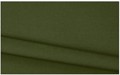
600D Polyester
The budget workhorse found on many commercial big-name brand bags. It's cheap and reasonably strong, but quality can vary wildly. A great starting point, but always choose a PU-coated version over the heavier, less pleasant PVC-coated kind for increased strength.
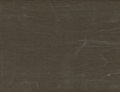
Cotton Canvas
For a traditional, heritage look. Usually treated with wax for water resistance, it ages beautifully but is significantly heavier and weaker than modern synthetics.
Halley Stevensons (UK) Big Duck Canvas (US)Stretch & Utility Fabrics
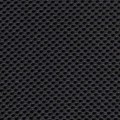
3D Spacer Mesh
The padded, breathable mesh you see on shoulder straps and back panels. It provides cushioning and promotes airflow. 3mm is a common and versatile thickness.

Stretch Mesh (Powernet, Venom, Ultra-Stretch)
Essential for those big front pockets and water bottle holders. Powernet is a durable, affordable option. For the ultimate in tear-resistance, look at premium meshes like Challenge Ultra Stretch, which incorporate UHMWPE fibers. They have less stretch but are incredibly tough.
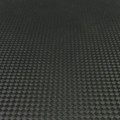
Heavy-Duty Reinforcement: PVC & Hypalon
These are specialists for extreme abrasion zones. Heavy PVC/Truck Tarp is very durable, waterproof, and cheap, but heavy. Hypalon/CSM is a synthetic rubber that's lighter and more refined. It's the expensive gold standard for bike bag attachment points.
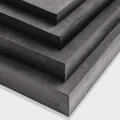
Closed Cell Foam (EVA)
The padding of your shoulder straps and hip belts. Evazote is a premium option, but high-density EVA foam from cosplay suppliers works great too.
Apparel & Insulation
Fabrics designed to be worn, offering breathability, comfort, and weather resistance.
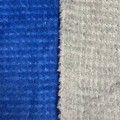
Polartec® Alpha® Direct
A revolutionary active insulation layer. It's a fuzzy, high-loft fleece without a face fabric, making it phenomenally breathable. Perfect as a midlayer for high-output activities like hiking and climbing, as it dumps heat and moisture instantly. It's often paired with a lightweight, wind-resistant shell.
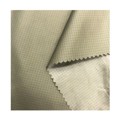
Breathable Nylon Shells (10D - 20D)
Featherlight and tightly woven, these fabrics are the perfect outer layer for wind shirts, quilts, and sleeping bags. They offer surprising wind and light precipitation resistance while remaining highly breathable and packable. Look for options with a calendered finish for extra wind resistance, and downproof finishes for use with feathered insulation.
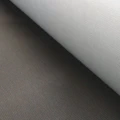
Waterproof Breathable Fabrics (WPB)
Laminated fabrics commonly used for waterproof coats and trousers, with Gore-Tex being the main household name. They consist of 2, 2.5 or 3 layers including a membrane to allow moisture to breath out while still remaining waterproof. If a fabric can be both waterproof and breathable is strongly debated.
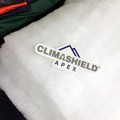
Climashield APEX Insulation
The gold standard for sheet-style synthetic insulation. It's a continuous filament, which means it won't clump and is super easy to work with, as it can just be sandwiched between your shell fabrics.
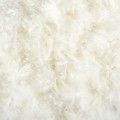
Down Feather Insulation
The best weight to efficiency insulation available. Clumps when wet (some down comes treated for water repellency), and can have ethical issues. Look for RDS (Responsible Down Standard) branding for suppliers that make some attempt to be ethical, but do your own research if this is a concern of yours.
Webbing & Grosgrain
Webbing is super important for your bag's functionality, used for everything from compression straps to gear loops. Choose wisely!
- Polypropylene: The cheap stuff from generally found in craft stores. It's lightweight and floats, but it feels coarse, fades in the sun, and unravels easily. Fine for non-critical uses, but there are better options.
- Nylon: The standard for high-quality gear. It has a soft, supple hand-feel, a tight weave, and excellent grip in buckles. It does absorb some water and can stretch slightly when wet, but for most pack applications, it’s the best all-rounder.
- Polyester: Stiffer and more UV-resistant than nylon, and it doesn't absorb water. An excellent choice for any application where stretch is undesirable, like hammock suspensions.
- Grosgrain Ribbon: Technically a light-duty webbing. It’s perfect for binding raw edges, creating pull-tabs, and making small gear loops. While not for load-bearing straps, it's an essential part of any MYOG toolkit.